Herausforderungen bei Industrial IoT und Digitalisierung im deutschen Maschinen- und Anlagenbau
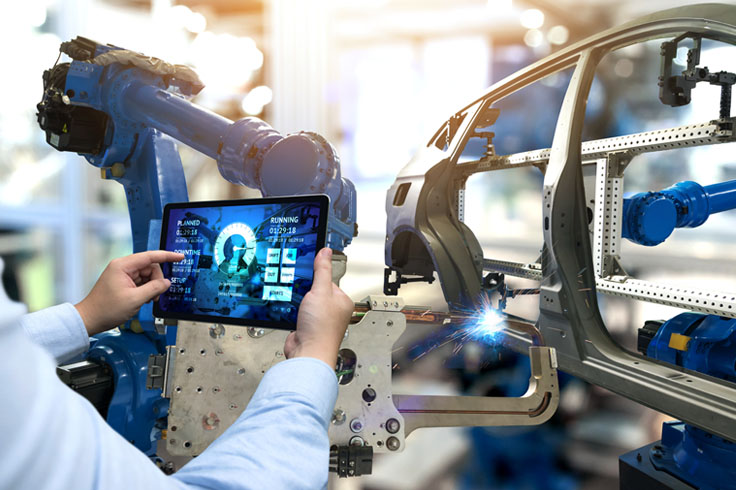
IT-Leiter stehen gerade im Maschinen- und Anlagenbau vor einigen Herausforderungen. Bis vor wenigen Jahren wurde die Automatisierung und Digitalisierung als Jobkiller in Medien verschrien. Mittlerweile hat sich flächendeckend die Notwendigkeit verankert. Neben dem Top-Management müssen auch die Mitarbeiter an das Internet of Things (IoT) bzw. Industrial Internet of Things (IIoT) herangeführt werden, was im Rahmen von Change-Management-Maßnahmen erfolgen kann. Die Entwicklung eines reinen Maschinenherstellers hin zu einer Mischung aus einem Service-via-Software- und Produktionsunternehmen fordert die Einführung und Entwicklung einer zukunftsfähigen Unternehmens- und Mitarbeiterkultur.
Smart Products und Smart Services
Aufgrund des globalen Wettbewerbsdrucks steht der deutsche Maschinenbau vor der großen Herausforderung, sich von einem reinen Maschinenproduzenten zum digitalen Lösungsanbieter zu entwickeln. Hierfür ist zum einen die Erweiterung bei den Wettbewerbsfaktoren von kostenintensiven Einsatzkomponenten oder Rohmaterialien hin zu Informationstechnologie und Datenanalyse zu nennen. Zum anderen steigt auf der Kundenseite die Nachfrage nach ganzheitlichen und vernetzten Produktions- und Automatisierungslösungen. Ein Großteil der konservativen Maschinenbaubranche verfolgte jedoch lange den klassischen produktorientierten Ansatz. Noch vor einigen Jahren spielte die Digitalisierung nur für rund ein Fünftel der in Studien befragten Unternehmen eine zentrale Rolle für den eigenen Erfolg. Durch vertragliche Regelungen können Maschinenhersteller die Maschinen, die bei ihren Kunden in Betrieb sind, über verschiedenen Wege wie zum Beispiel einem Unified Namespace (UNS) mit dem Internet verbinden. Die Daten, die während des Maschinenbetriebs beim Kunden gesammelt werden, werden somit auf dem Unified Namespace zusammengetragen. Die an das Internet angebundenen Maschinen werden Smart Products genannt. Die Daten werden durch die intelligente Verarbeitung (Analyse) in der IoT-Anwendung zu Smart Data verwandelt. Basierend auf Smart Data hat der Maschinenhersteller die Möglichkeit, sich selbst und seinen Kunden Produktivitätsvorteile zu generieren
ERP als Datendrehscheibe
Als Datendrehscheibe hat ein modernes ERP-System einen großen Radius: Die Daten können direkt von den Produktionsmaschinen aus, aus Geschäftsprozess-Daten oder sogar von außerhalb des Unternehmens gesteuert werden. Ein Beispiel dafür ist das Konzept der Smart Maintenance (intelligente Wartung), die sogar als Dienstleistung an Kunden eines Maschinenherstellers verkauft werden kann. Je vielfältiger die Systeme, desto wichtiger ist ein modernes, offenes und flexibles ERP-System, das Funktionalitäten von Künstlicher Intelligenz, IIoT und AR integriert hat
und so den Umgang mit Daten automatisiert und diese Daten entsprechend sammelt und verwaltet. Dies umfasst Daten aus verschiedensten Quellen wie IT-Systemen, Transaktionen und den unterschiedlichsten Abteilungen eines produzierenden Unternehmens, die im ERP zentral via Frameworks gesteuert werden. Eine zentrale Datenhaltung in einem intelligenten ERP-System ist die beste Grundlage, um Daten als Rohstoff adäquat zu nutzen. Moderne ERP-Systeme werden daher als Smart Business Process Hub konzipiert. Entscheidend für die Zukunftsfähigkeit eines ERP-Systems ist Wandlungsfähigkeit hin zu Micro-Services. Eine hochgradige Interoperabilität ermöglicht die Plattform-Fähigkeit eines ERP-Systems, das die Digitalisierung der Unternehmensprozesse adäquat unterstützen kann.
Mit Industrial IoT Mehrwert schaffen
Der Maschinenhersteller hat die Möglichkeit, die Maschinen, die er seinem Kunden verkauft hat, an das Industrial IoT anzubinden. Dadurch können sämtliche Daten aus dem Maschinenbetrieb in Echtzeit auf einen zentralen Datensammelpunkt wie einem Unified Namespace übertragen und in weitere Systeme, bspw. in das MES eingespeist werden. Der Unified Namespace ist eine virtuelle Ebene, auf der Daten aufbereitet und für weitere Applikationen zur Verfügung gestellt werden. Die Maschinenanbindung sowie die Datenübertragung können in unterschiedlichen Vertragsformen mit dem Kunden vereinbart werden. Auf Basis der gesammelten Daten kann der Maschinenhersteller sowohl für seine Kunden als auch für sich selbst einen Mehrwert generieren. Im Fokus steht die Produktivitätssteigerung der Kundenprozesse sowie der internen Unternehmensprozesse. Folglich kann zwischen einer kundenzentrierten Sicht und einer wertschöpfungszentrierten Sicht auf die Digitalisierung unterschieden werden. Einerseits hat der Maschinenhersteller die Möglichkeit, dem Kunden Software zu verkaufen. Dieses Geschäftsmodell wird als Software-as-a-Service-Modell bezeichnet. Basierend auf den Daten kann der Maschinenhersteller Applikationen entwickeln und dem Kunden zur Verfügung stellen. Die Applikationen unterstützen den Kunden, die Maschinen und Anlagen effizienter zu betreiben. Andererseits kann der Maschinenhersteller dem Kunden neue, kundenspezifische Dienstleistungen und auf den individuellen Bedarf des Kunden zugeschnittene Geschäftsmodelle wie Pay-per-Use anbieten. Die datenbasierten Dienstleistungen werden auch Smart Services genannt und beziehen sich in der Regel auf die Datenauswertung, das Wartungssystem und auf die Zustandsüberwachung der Maschinen beim Kunden. In diesem Rahmen ist vor allem das Thema vorausschauende Wartung (Predictive Maintenance) präsent. Auf Basis der Daten ist es dem Maschinenhersteller möglich, den Kunden frühzeitig über notwendige Wartungsarbeiten zu informieren, sodass Maschinenstillstände vermieden werden können.
Der Maschinenhersteller kann mit Industrial IoT sein Ersatzteilgeschäft verbessern. Mit Hilfe des vorausschauenden Wartungskonzepts ist der Verschleiß einer Maschine frühzeitig erkennbar, wodurch dem Kunden eine entsprechende Service-Leistung, inklusive benötigter Ersatzteile, mit einer termingerechten Lieferung angeboten werden kann. Somit wird eine höhere Wertschöpfung erzielt, die Abwanderung des Kunden zum Wettbewerb vermieden und die Kundenzufriedenheit erhöht. Die bessere Einschätzung der erwarteten benötigten Ersatzteile führt zu einem verbesserten Lagerbestand des Herstellers, der zeit- und mengentechnisch durch IIoT optimiert wird. Die Daten dienen dem Maschinenbau zur Verbesserung der Maschinenherstellung. Indem er Informationen über die Maschinen während des Betriebs beim Kunden erhält, ist die Identifizierung der Maschinenschwachstellen sowie der Verbesserungspotenziale möglich. Die Berücksichtigung des neu generierten Wissens in der Maschinenentwicklung kann zur Qualitätsverbesserung ganzer Maschinengenerationen führen. Weitere Mehrwerte, welche sich durch das Zusammenspiel aus Industrial IoT und ERP als Datendrehscheibe erzielen lassen, sind zum Beispiel kürzere Produktionszyklen für Produkte und dadurch niedrigere Kosten in der Produktion.
Ein weiterer Vorteil der Anbindung an das Internet ist ein früheres Erkennen von Fehlern im Produktdesign, so dass spätere Eingriffe in der Produktion vermieden werden können. So lassen sich Kosten reduzieren. Auch der Ausschuss in der Produktion kann deutlich verringert werden, weil Rückmeldungen von Kunden und Produktion in Echtzeit übermittelt werden und so Änderungen an der Produktionslinie schneller durchgeführt werden können.
IoT umsetzen im Maschinen- und Anlagenbau
Mit IoT-Technologien können Unternehmen ihre Prozesse im Maschinen- und Anlagenbau deutlich optimieren und an den wichtigsten Stellschrauben drehen. Dabei greifen einzelne Lösungen wie ERP, BI, MES, Retrofit und Asset Tracking wie Zahnräder ineinander. Wenn Daten das neue Öl sind, ist IoT die Technologie zur Förderung, Veredelung und zugleich zur Nutzung – also Bohrturm, Raffinerie und ölbetriebene Maschine in einem. Die wichtigsten Tipps wurden in einem Whitepaper zusammengefasst: IoT umsetzen im Maschinen- und Anlagenbau:
Erfahren Sie wie MES Daten aus ERP, Maschinen und Industrie 4.0 zusammenführt!
Über Comarch IoT MES
Comarch IoT MES ist ein umfassendes System, das im SaaS-Modell (Software as a Service) oder als kundenspezifische, dedizierte Lösung bereitgestellt wird. Es besteht des Weiteren aus einer Echtzeitauslese und Aufbereitung der Daten aus Produktionsanlagen (SPS und Sensoren) mit Empfängern (Comarch IoT Hubs). Diese Empfänger sind mit dem Unified Namespace (UNS) verbunden, der als Datensammelpunkt für Industrie-4.0-Lösungen dient. Der UNS basiert auf einem internationalen Standard und ermöglicht eine modulare Integration von verschiedenen Industrie-4.0-Lösungen. Durch den UNS werden die Daten aus den verschiedenen Datenquellen in eine standardisierte und gemeinsame Datenstruktur überführt. Das IoT basierte MES von Comarch umfasst Funktionen und Komponenten wie Hardware-Integration, Echtzeit-OEE-Berechnung, NOK-Management, digitalen Anweisungen, Benachrichtigungen sowie eine Integration mit Comarch ERP Enterprise und Comarch Business Intelligence.